In this blog, we're guiding you through the essentials of wire rope maintenance and how to carry out proper rope inspection - while finding the best products that provide excellent lubrication for wires and strands.
Steel wire ropes are an essential component of equipment for a wide range of industries, and are relied upon for excellent performance while handling bending stress. These ropes are composed of multiple steel rope strands that are formed around a core, and ensuring these ropes are taken care of properly is a top priority.
In this blog, we're guiding you through the essentials of wire rope maintenance and how to carry out proper rope inspection - while finding the best products that provide excellent lubrication for wires and strands.
“Penetrating lubricant is applied to the core of the wire rope during the manufacturing process, which reduces wear and increases service life.”
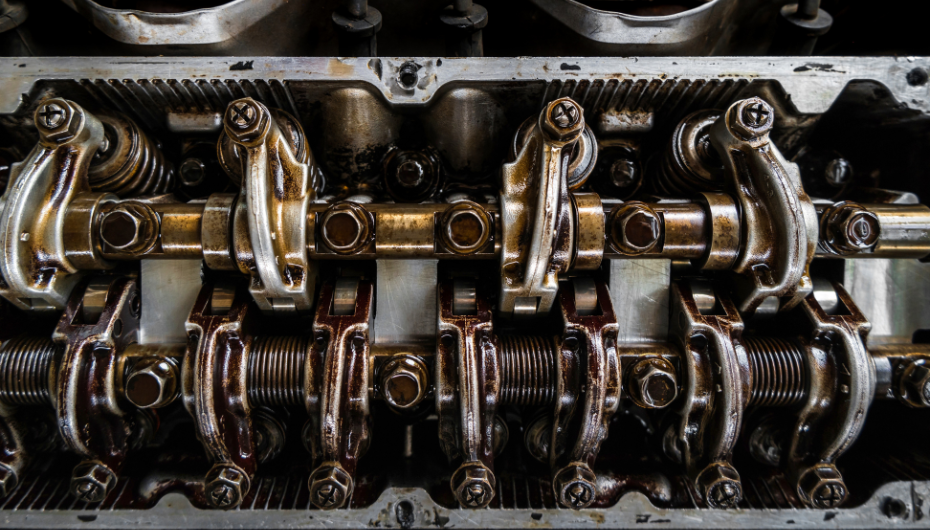

Over time, wires will start to break down and the rope must be replaced, This is inevitable due to stretching bending or weather conditions, however, keeping up proper maintenance will increase the lifespan of your ropes and reduce the risk of broken wires.
The two main benefits of using wire rope grease for lubrication and protection are:
- Reduce friction as the individual wires move against each other.
- Offers corrosion protection and lubrication for the core of the wire and other surfaces.
These benefits provide less friction to reduce wear and also enhance the day-to-day performance of your wire ropes by protecting against corrosion. Different wire ropes are subject to different conditions, which means some applications require more lubrication.
For example, wire ropes used for carrying heavy loads such as cranes or hauling equipment are subject to demanding applications which means they are subjected to more wear. These components need to be lubricated more often and knowing how to keep up maintenance is essential - particularly when it comes to preventing internal corrosion.
1 - Outside Elements And Weather
Everything from heat to wet environments can cause damage to your wire ropes over time, causing them to corrode from the inside. This weakens the rope and increases the risk of damage, and regular lubrication helps keep corrosion at bay.
2 - Wear and Tear
A certain amount of wear cannot be avoided, especially for heavy-duty wire ropes. Proper cleaning and lubrication extend the life of your components and stop wear and tear from damaging your equipment.
3 - Outside Elements And Weather
Everything from heat to wet environments can cause damage to your wire ropes over time, causing them to corrode from the inside. This weakens the rope and increases the risk of damage, and regular lubrication helps keep corrosion at bay.
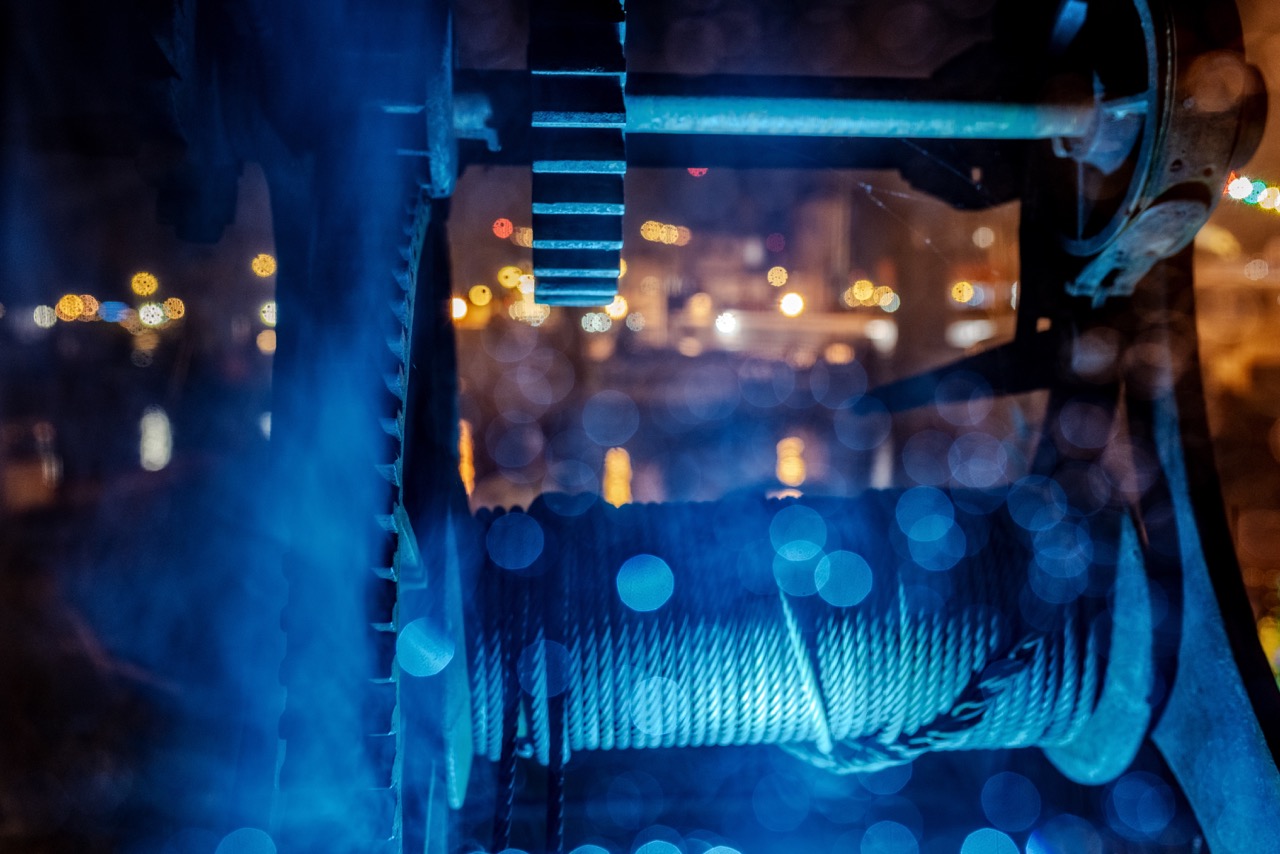
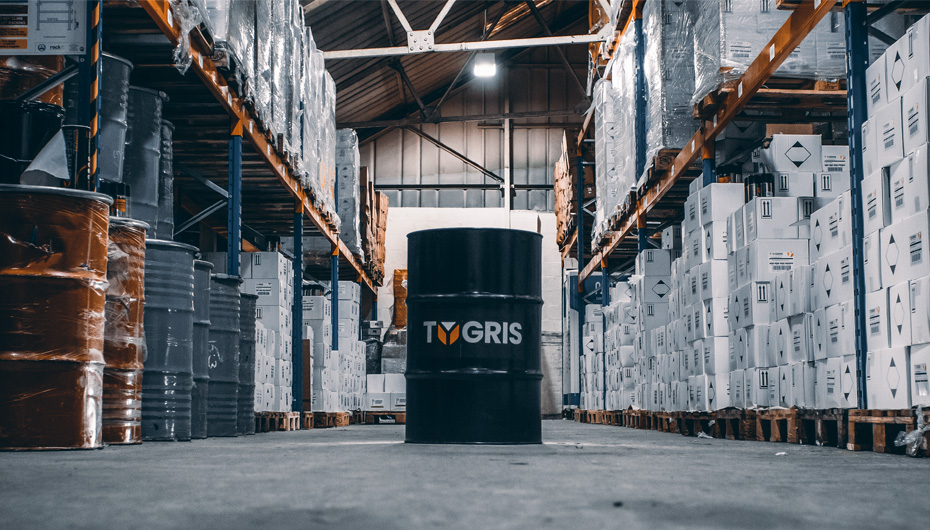
How To Spot Problems With Your Ropes
Applying grease according to a set schedule rather than a need can cause issues for your application and lead to an increased risk of breakdowns. That is why knowing how to visually inspect the ropes and determine if reapplication is necessary is so essential.
There should be some residue, with a visible lubricating film of oil. If you cannot see this film then your wire rope will require an immediate application of lubricating grease. However, if there is a visual film without any oily residue, the ropes require immediate cleaning and lubrication.
this widget to input text into the page.
TYGRIS Wire Rope Grease
This specialised lithium grease is designed for ropes subjected to extreme load conditions. Perfect for marine applications such as dockside cranes, this semi-fluid wire rope grease provides excellent protection both internally and externally.
Leaves a water-resistant film to ensure a longer component life and longer lubrication intervals.
Gives fantastic cover power for economic usage.
Reduces wear between the strands of the rope.
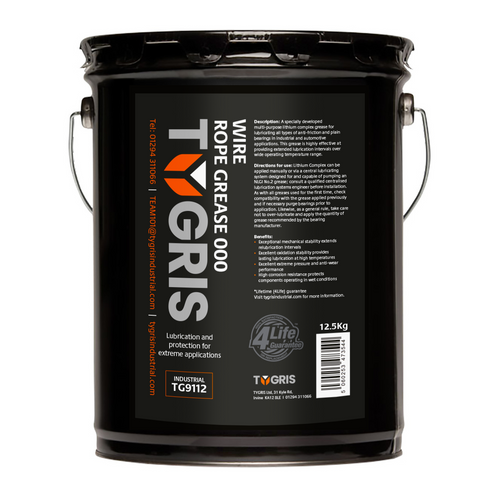
TYGRIS Bio-Degradable Rope Lubricant
If you are seeking a sustainable solution for your wire ropes, then this bio-degradable grease is an excellent choice. A greener alternative to conventional grease, this solvent-free lubricant can be used in all rope applications and help to prevent corrosion.
Provides an environmentally acceptable solution.
Gives fantastic protection internally and externally to extend the life of wire ropes.
Water-resistant properties extend lubrication intervals.

TYGRIS Chain & Wire Rope Lubricant
An ideal solution for anyone looking for a way to streamline their lubricants, this molybdenum disulphide-reinforced aerosol can be used to lubricate and protect wire ropes and drive chains from corrosion and wear.
Can be used on chain blocks, drive chains, forklift chains, and wire ropes
Enhanced with extreme pressure additives for heavy loads.
Leaves behind a thin film to prevent corrosion.
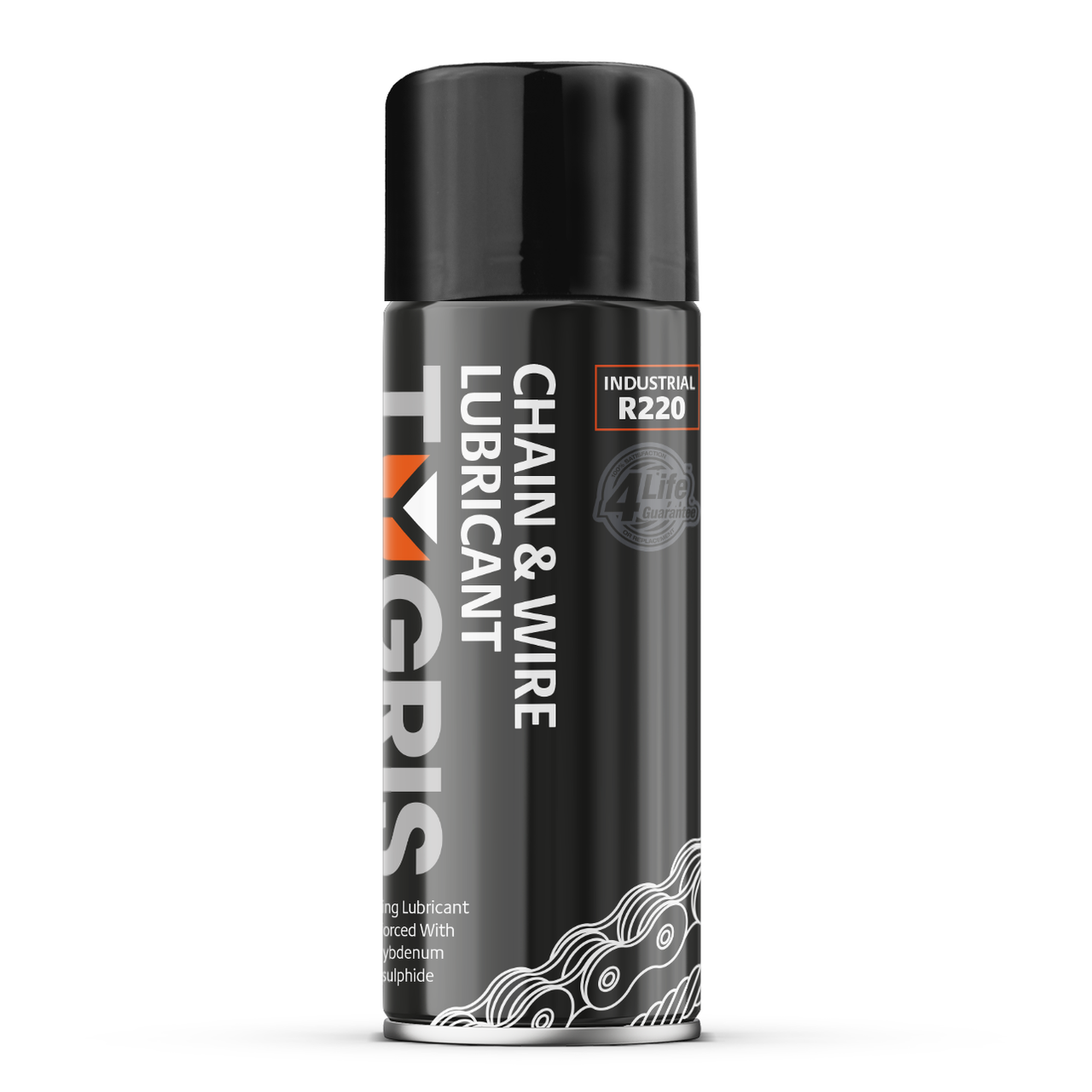